The Science Behind Porosity: A Comprehensive Overview for Welders and Fabricators
Comprehending the elaborate devices behind porosity in welding is vital for welders and fabricators making every effort for remarkable workmanship. From the composition of the base products to the details of the welding procedure itself, a wide range of variables conspire to either intensify or reduce the presence of porosity.
Understanding Porosity in Welding
FIRST SENTENCE:
Assessment of porosity in welding discloses essential insights into the stability and quality of the weld joint. Porosity, characterized by the visibility of cavities or voids within the weld metal, is an usual issue in welding processes. These spaces, otherwise correctly resolved, can jeopardize the structural stability and mechanical residential or commercial properties of the weld, resulting in possible failings in the completed item.
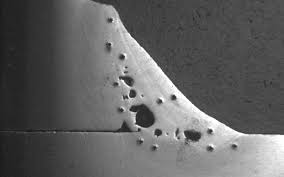
To spot and quantify porosity, non-destructive testing approaches such as ultrasonic screening or X-ray evaluation are usually employed. These techniques enable for the identification of internal flaws without endangering the stability of the weld. By analyzing the dimension, form, and circulation of porosity within a weld, welders can make informed choices to enhance their welding procedures and attain sounder weld joints.

Elements Affecting Porosity Formation
The incident of porosity in welding is affected by a myriad of elements, varying from gas securing effectiveness to the details of welding specification setups. Welding specifications, consisting of voltage, present, take a trip rate, and electrode kind, also effect porosity formation. The welding strategy utilized, such as gas metal arc welding (GMAW) or secured metal arc welding (SMAW), can affect porosity development due to variants in warm distribution and gas protection - What is Porosity.
Impacts of Porosity on Weld High Quality
Porosity formation dramatically jeopardizes the architectural honesty and mechanical buildings of welded joints. When porosity exists in a weld, it develops gaps or dental caries within the material, lowering the overall toughness of the joint. check this site out These gaps work as tension concentration factors, making the weld a lot more at risk to cracking and failing under lots. The presence of porosity likewise weakens the weld's resistance to corrosion, as the trapped air or gases within the spaces can respond with the surrounding setting, resulting in degradation gradually. In addition, porosity can prevent the weld's ability to withstand pressure or impact, more jeopardizing the general high quality and integrity of the bonded structure. In vital applications such as aerospace, auto, or architectural buildings, where safety and resilience are vital, the destructive impacts of porosity on weld quality can have serious consequences, stressing the significance of lessening porosity through appropriate welding techniques and treatments.
Techniques to Minimize Porosity
In addition, utilizing the appropriate welding criteria, such as the right voltage, current, and travel speed, is crucial in preventing porosity. Keeping a constant arc length and angle during welding also assists decrease the likelihood of porosity.

Making use of the ideal welding strategy, such as back-stepping or using a weaving movement, can also assist distribute heat uniformly and decrease the possibilities of porosity formation. By implementing these methods, welders can effectively lessen porosity and generate top quality bonded joints.

Advanced Solutions for Porosity Control
Implementing innovative innovations and ingenious approaches plays a crucial role in attaining exceptional control over porosity in welding processes. In addition, employing advanced welding methods such as pulsed MIG welding or browse around this web-site modified atmosphere welding can likewise assist minimize porosity issues.
An additional innovative option entails the usage of sophisticated welding devices. Utilizing equipment with integrated attributes like waveform control and innovative power sources can improve weld quality and decrease porosity threats. Additionally, the application of automated welding systems with exact control over criteria can significantly decrease porosity defects.
Additionally, incorporating sophisticated monitoring and inspection technologies such as real-time X-ray imaging or automated ultrasonic screening can aid in finding porosity early in the welding see this procedure, enabling prompt corrective actions. Generally, incorporating these innovative services can significantly boost porosity control and enhance the overall high quality of bonded components.
Verdict
In conclusion, recognizing the scientific research behind porosity in welding is essential for welders and fabricators to generate premium welds - What is Porosity. Advanced remedies for porosity control can better improve the welding procedure and guarantee a strong and dependable weld.